Haas tanneries
Based in Alsace, the Haas tanneries have been producing exceptional leathers for their customers, including some of the French leading luxury brands, for almost 200 years.
We decided to come and meet this supplier since day one to find out more about the world of tanning.
Philippe Keller and Sébastien Croidieu are respectively Operations Director and Sales Director for Haas tanneries. They both have decades of experience in the tanning industry, both in France and Europe.
They talk to us about their tannery, their business... and leather, of course!
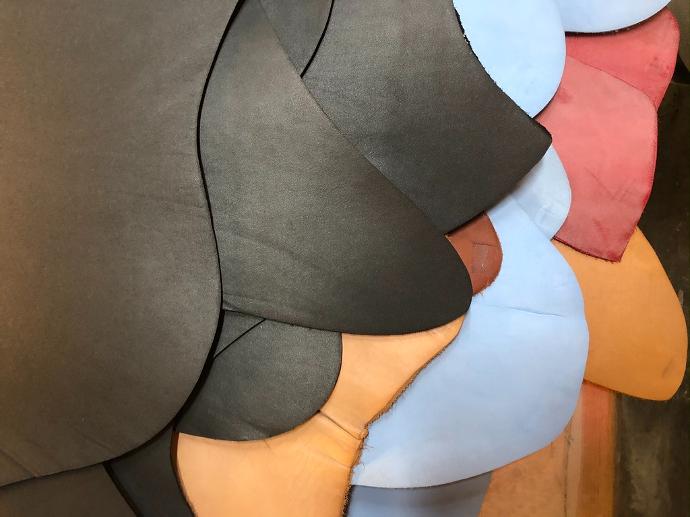
What drew you to the tanning industry, and what do you particularly like about it?
What are the defining characteristics of Haas tanneries?
While some tanneries process calf and bovine hides, and smaller hides are handled by tanneries, Haas tanneries only process calf hides. We mainly use a double tanning process, chrome and vegetable, as described in our Novonappa® product. The tannery takes charge of the entire process (around 6 weeks), from the purchase of hides from slaughterhouses to the finished leather. Last but not least, quality control is an integral part of the whole cycle, so that we can produce high quality leathers.
Can you tell us a little more about the process of transforming a hide into leather?
Of course ! It's an extremely complicated and time-consuming process.
It begins with the river cycle, which removes the hair from the hide and cleans it.
Tanning then transforms the hide into leather, making it rot-proof. The dyeing process gives the leather its color.
Next comes wet currying, which removes moisture from the hide. Dry currying softens the hide, giving it its final characteristics. At this stage, the leather is semi-finished.
Finally, the aim of all finishing operations is to give a leather a visual appearance by adding all the technical characteristics desired by the customer in his specifications (resistance to water, light, rubbing, etc.).
Earlier, you spoke of our focus on quality. Can you tell us more about that?
Hides are inspected at every stage of the production process, and more specifically at four stages: raw hides, tanned hides, semi-finished hides and finished hides before being sent to our customers. For example, after tanning, the first quality control enables us to orientate the hides (according to scratches, pitting, etc.) towards the different articles we produce. The final check takes place before shipment, to ensure that the leather matches the customer's complete specifications.
At adapta_, we work with deadstock of unused leather. Can you tell us more about deadstocks ?
In terms of quality, it's exactly the same as the leather used by our customers.
In our production cycle, we regularly have surpluses, or leathers that don't meet customer expectations for various reasons (color, gloss, thickness, etc.). These leathers are then made available to adapta_ and sold to other designers & brands who use smaller quantities. It's a virtuous upcycling circuit that gives everyone access to our leathers.
Can you tell us about the two types of tanning: vegetable and chrome?
Then, at the beginning of the 20th century, chrome tanning overtook vegetable tanning, which was more complex to implement.
However, new molecules currently being researched will enable us to reduce or eliminate the use of chromium in the years to come.
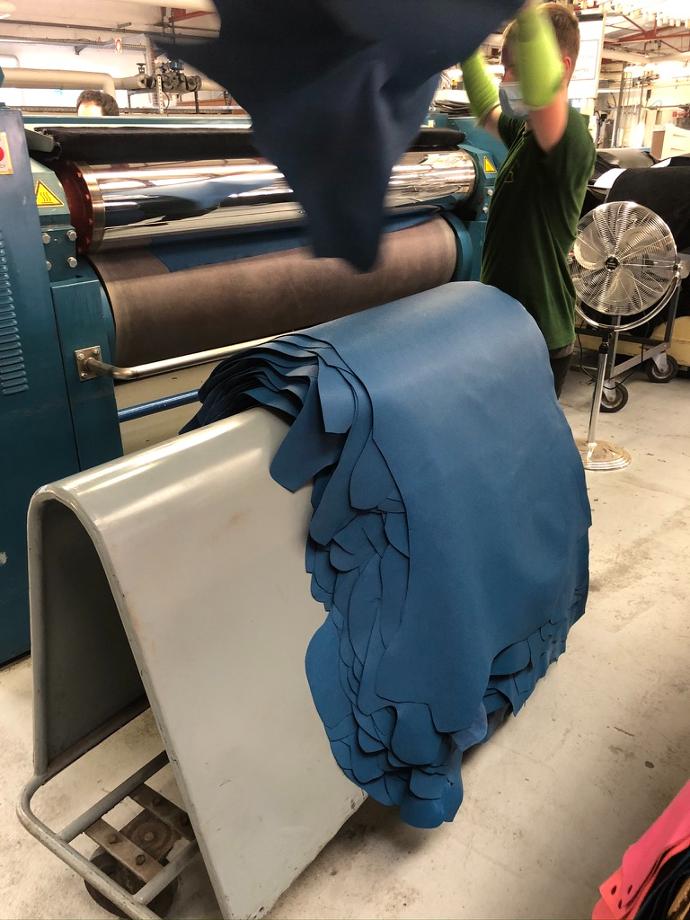
Can you tell us something about the current debate on the environmental impact of these two types of tanning?
One of these is a life-cycle analysis of tanning, and we are awaiting the results.
We also often talk about water pollution caused by chrome tanning. Can you tell us about your infrastructures and facilities set up in-house to comply with all French and European standards?
After treatment in our plant, the water is sent to the municipal wastewater treatment plant for overall treatment in the same way as household wastewater.
Our challenge is to reduce the use of water, and to reduce or eliminate the use of chromium and solvents. In addition, our finishing processes have been in an aqueous environment for several years now.
Tanning (like other industries) does use chemicals. So we have to be particularly careful. Our industry is monitored by government agencies (the DREAL), where the specifications to be respected in terms of discharge are extremely precise and rigorous. Our effluents are monitored on a daily basis.
Tanning is an industry that has evolved a great deal in recent years, and will certainly evolve even more rapidly in the years to come.
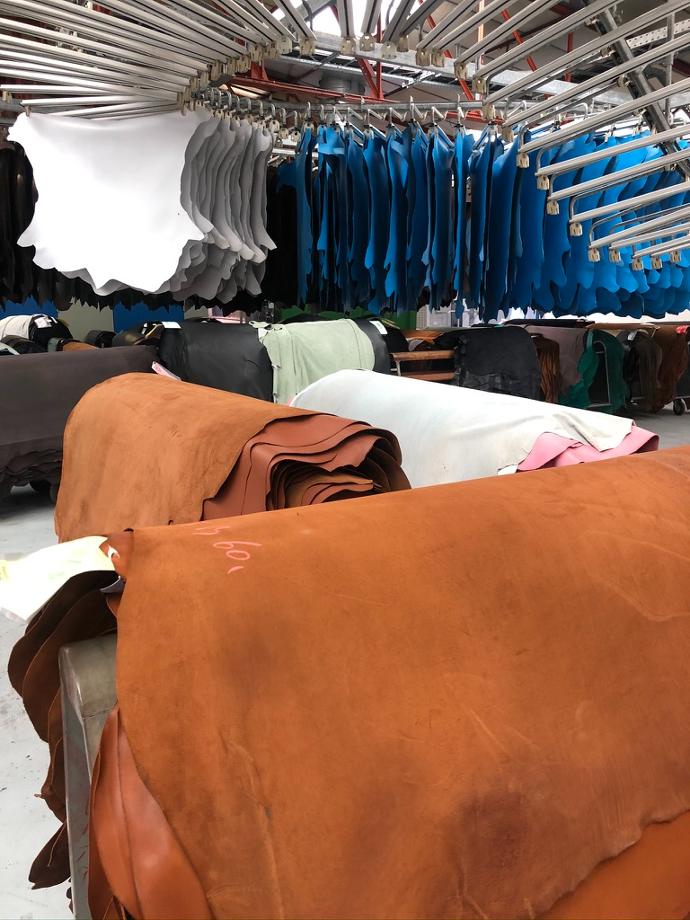
It's often said that leather that has been tanned for shoes can be used for leather goods, but that the reverse is not possible. Is that true ?
Generally speaking, yes, but there are many counter-examples. For example, Novonappa ® is a leather with a very natural look (which is part of what it's famous for). But this implies sensitivity to light and fragility to scratches, and despite this, it is used for leather goods.
When it comes to shoes, it all depends on what you want to do with them: a little ballerina with leather that doesn't change? A shoe with a sportier leather that will wax and patina? Depending on this, you'll need a leather that's adapted to your needs (elasticity, for example). So it's hard to answer yes or no, and that's why advice is so important.
I wanted to come back to your collaborations with your customers... We've talked about the big luxury houses, but I often see small players who are blissfully impressed by your leathers, but who have the impression that you don't want to work with them. Is this linked to your production methods, which require minimum quantities?
Indeed, this is not a commercial constraint but an industrial one, in view of our quality requirements. We have equipment, particularly for tanning and dyeing (fulling machines), for which we need to have sufficient mass effect to achieve the expected quality. That's why it's so complicated to manufacture very small volumes: you'd need different equipments at different costs. So it's really an industrial constraint. We'd be delighted to work with small designers, but unfortunately we can't meet their direct demand.
You've been working with adapta_ for 2 years now, and your leathers are among the top 10% in France. Can you tell us why you decided to work with us?
We know that our industrial constraints can be a problem when it comes to giving young designers access to our leathers. What's interesting about your approach is that, through your intermediary, you can provide access. It's an approach that really interested us, because we thought it made a lot of sense: reusing high-quality materials and giving them a second life. It's extremely interesting because it gives a new dimension to unused leather and opens up a market to which we didn't have access before.
What are your plans for the future of Haas tanneries, even in these uncertain times?
We are indeed going through a period of uncertainty, and it's very difficult to plan for the short and medium term. We have to be reactive, flexible and creative, and offer designers more and more new products. Our R&D teams are constantly working on new projects.